Why Process Parameters Matter in Robotic Metallizing
Unlock the full potential of metallizing
At Clemco Denmark, we know that even the most advanced thermal spray systems are only as good as the process parameters them selves.
From tower sections for wind turbines to structural steel beams and complex casted parts, thermal spray coatings play a vital role in ensuring corrosion protection and longevity. But to unlock the full potential of metallizing, precise control is everything and especially when it comes to robotic applications.
The Hidden Power of Process Parameters
Even with perfect surface preparation and an optimal coating thickness, thermal spray coatings can still fail if the process parameters are off. Variables such as temperature, spray distance, and deposition rate directly affect coating quality. In manual operations, these parameters are vulnerable to inconsistencies. That’s why automation is key.
At Clemco, our robotic metallizing solutions - including our dual-arm robot for structural steel, gantry and wall systems for castings, and custom carts for tower sections - are designed to maintain perfect consistency in these critical parameters. The result? Higher quality, longer-lasting coatings, and fewer costly reworks.
Key Parameters and How Robotics Improve Them
1. Flame or Arc Temperature
For reliable adhesion and low porosity, the coating material must be properly melted before application. Overheating causes oxidation; underheating leads to poor bonding.
- With Clemco robots, temperature control is built into the process. Integrated sensors and some specific spray controlling tools allow real-time monitoring and data feedback eliminating guesswork.
2. Particle Velocity
Velocity affects how particles deform and bond with the substrate. Manual setups struggle to maintain this consistently. Too low, and particles bounce. Too high, and they splash or fracture.
- Our automated systems ensure precise, repeatable velocity through stable gas flow, calibrated nozzles, and optimized spray paths. These are all critical parameters when coating large components like bridge sections or wind turbine towers.
3. Spray Distance
Inconsistent spray distance is a major cause of uneven coatings, porosity, and delamination.
- Robotic arms and gantries maintain a constant distance from the substrate, even on curved or angled surfaces using programmed paths and adjustable jigs. This is particularly beneficial when metallizing complex castings or rotating tower sections.
4. Deposition Rate
Too fast, and layers don’t bond well. Too slow, and production is inefficient.
- Our solutions are engineered for optimal feed rates. With programmable logic, robots adapt deposition rates to the geometry and material, achieving uniform layers without excessive material waste.
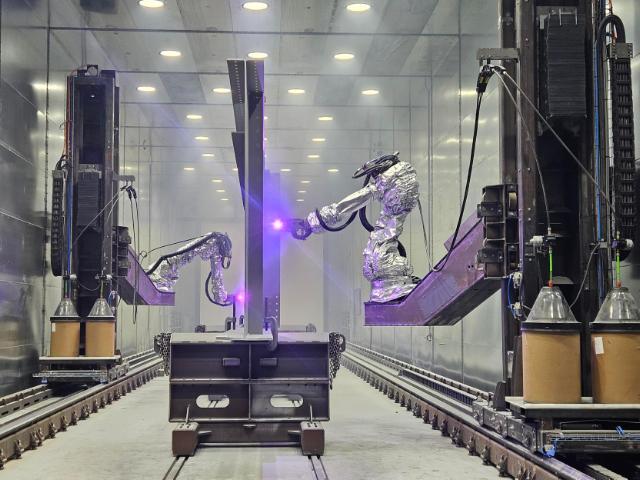
Why robotic systems are worth it
Thermal spray is a science, but human variability introduces risk. That’s where robotic systems show their worth:
Precision: Every pass is identical, every time.
Reduced Maintenance Errors: Wear on components like nozzles or cables is easier to detect with diagnostic alerts.
Operator Oversight, Not Intervention: Skilled operators supervise rather than manually adjust settings during the actual process.
Data-Driven Insights: Parameters can be logged, analyzed, and refined over time.
From automated metallizing of offshore wind tower sections to structural steel used in bridges and buildings, the robots from Clemco Denmark ensure the coating process is consistent, no matter how large or complex the parts are.
Common Defects Our Systems Help Prevent
Manual or poorly calibrated thermal spray processes often lead to:
- Porosity from unmelted or cool particles
- Oxidation from excessive heat or air exposure
- Delamination from uneven bonding
- Uneven Coatings from fluctuating spray paths
All of these challenges are minimized when using Clemco Denmark automated metallizing systems with tight control over process variables.
Investing in the Future of Metallizing
Success in thermal spray coatings depends on more than the wire or the equipment. It is all about how precisely the process is controlled. Clemco Denmark's robotic systems are designed to help customers:
- Minimize coating failures
- Reduce rework and material waste
- Boost productivity with consistent, high-quality output
- Achieve faster ROI with reduced operational costs
Whether you are coating wind tower sections, structural beams, or cast components, the key is consistency, and that is what you get when we deliver a robotic solution.